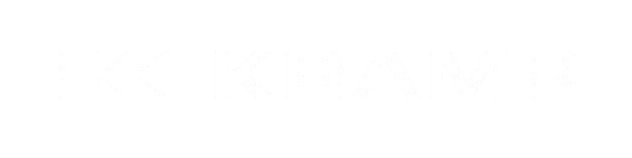
Kramp was looking for a single provider for all its logistics flows and associated processes. With IDS, it now has just that.
Mitsubishi Engineering-Plastics Corporation (MEP) has been working with IDS since 2010. The relationship began as operational support to keep the plastics manufacturer’s day-to-day transportation operations running smoothly during a hectic transition period. Since then, it has evolved into a much deeper partnership that significantly reduces the workload within MEP’s Supply Chain & Customer Service department.
Headquartered in Japan, Mitsubishi Engineering-Plastics Corporation (MEP) is a leading global supplier of engineering plastics for applications such as automotive, lighting and electronics.
Tim Verbugt, General Manager Supply Chain & Customer Service at MEP’s European headquarters in Düsseldorf (Germany), explains: “When we identify a new area of demand, we develop new products and materials that match it. Or we work with customers to create a customer-specific application that meets their needs.
For example, this could be a color – most people think ‘white’ is just ‘white’, but you would be amazed at how many different shades of white there are…”
Seamless transition
In 2010, MEP and DSM were involved in an exchange agreement; MEP acquired DSM’s European polycarbonate business in exchange for DSM’s acquisition of MEP’s polyamide business in Japan/Asia. Tim Verbugt then worked for DSM in Genk (Belgium), but made the switch to MEP three years after the exchange.
“Until then, MEP’s customer service was only responsible for arranging the import and transport of the products produced in Asia for European distribution. Suddenly, a supply chain department was added that is responsible for the purchase of raw materials, production planning and the transport of the end product manufactured in Belgium – polycarbonates – to customers in Europe and beyond.
This led to a number of major changes in the internal organisation in Düsseldorf,” tim recalls.
“That was the beginning of a hectic and stressful transition period. With so many internal organizational changes, it was initially a matter of “surviving” from day to day. A number of people switched from DSM to MEP, but it was still a challenge to build the supply chain and customer service almost from scratch.”
Against this background, IDS was a rock, as the company had been taking care of the logistics for DSM for several years. “That transport operation went so well that MEP saw no reason to change that,” says Tim.
“Thanks to IDS’ experience, they got things up and running quickly and properly within MEP – they even implemented a copy of the system for us – helping IDS to make the acquisition of the existing transport activities as smooth and seamless as possible.”
Tim readily admits that it took a number of years for the new supply chain and customer service operation to gain a foothold: “Business was going well and production was full, so the operational pressure was high. We didn’t have a lot of time to think about strategic optimization opportunities.”
Hands-on approach
Accidents can happen easily. In the event of a customer’s complaint about damaged goods, IDS first contacts the carrier to investigate the cause of the problem and to handle the crediting process.
“If there are repeated problems with a particular carrier, IDS will first address the problem independently. If necessary, we will visit the carrier together with IDS to discuss the situation and come to a solution.”
Indirect savings and strategic decisions
Another time-saving activity that IDS performs for MEP is around checking transport invoices before approving them for payment by MEP. “So every invoice we get from our carriers is checked.
IDS also takes care of the tender process for us,” says Tim. “They do most of the preparation work and send us a shortlist per country. We only have to make the final decision together, which saves us a lot of work.” Tim has no doubt that the fee paid to IDS for this level of service is money well spent:
“On paper, we could probably manage these activities ourselves. But we simply don’t have the time and resources for that, not to mention the necessary knowledge and capabilities.
Just communicating with so many different carriers already takes a lot of time. Now at IDS we have a single point of contact for transport and if there is something, they solve it for us. It’s the perfect solution!”
Tim sees no reason to change the relationship between MEP and IDS. “We are very satisfied with the guidance and expertise we receive from IDS. They work with different clients in our industry, so they have a lot of experience and a good understanding of our business. They also employ the right kind of people: young, proactive and not afraid to demand top service from carriers.
For one logistics project, we are currently analyzing how we can further optimize import activities from Asia. It’s interesting to see what else IDS could do for us, leveraging the large network ofcarriers and based on what we’ve learned together over the past seven years,” he concludes.